Auteur: Frans Morselt
De redactie van Boorn en Boerschop kreeg een artikel aangereikt dat een opstel bleek te zijn, geschreven door Frans Morselt jr. toen hij, in 1953 in Hengelo in de 2de klas van de HBS “De Grundel” zat. Bij navraag kwam naar voren dat Frans het opstel schreef naar aanleiding van een vraag van zijn leraar natuur- en scheikunde, de heer Willems, om een verhaal te maken over een chemisch of natuurkundig proces.
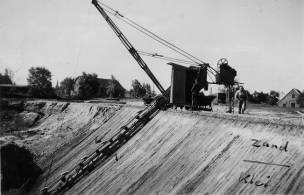
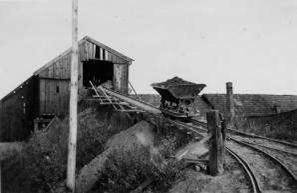
Het opstel
De grondstof voor de fabricage van bakstenen is de klei. Dit is meestal rivierklei. Ook wordt wel andere dan rivierklei gebruikt zoals de klei die in het ijstijdperk is afgezet. Zo zijn er veel fabrieken aan de grote rivieren te vinden en vooral zijn de stenen, geproduceerd langs de Waal, de “Waalklinkers”, zeer bekend. Deze fabrieken dragen een zeer behoorlijk steentje bij voor de aanleg van wegen.
Het graven van de klei
Het graven van de klei geschiedt in de kleiputten met behulp van een “bagger”, waarvan u een model in bedrijf kunt zien op de bovenstaande foto. De klei moet voor ongeveer ⅓ met zand vermengd worden, daar anders de stenen gaan scheuren tijdens het droogproces. De kleiput op de foto is zeer geschikt voor de vervaardiging van stenen. Is de klei te vet, dan moet er zand bijgevoegd worden, zoals dat bij sommige fabrieken het geval is, waar de klei direct onder de bodem zit.
Vervoer klei naar de fabriek
De bagger werpt de klei in “kipkarren”: dit zijn lorries die over rails lopen en waar een grote kipbak op bevestigd is. De hoeveelheid klei uit drie zulke kipbakken is voldoende voor de fabricage van ±1000 stenen. Wanneer de kleiput zich op enige afstand van de fabriek bevindt worden deze kipwagens door een locomotiefje getrokken. Bij de fabriek liggen wissels die de spoorlijn splitsen in drie gedeelten. Eén spoor voor het optrekken van de volle wagens, één spoor voor het terugvervoer van de lege wagens en één spoor waarop volle reserve wagens staan, indien de bagger eens mocht uitvallen, want het bedrijf moet doorgaan. De arbeiders werken in akkoord, dat wil zeggen dat ze worden betaald naar het aantal stenen dat ze per dag vervaardigen. De betaling geschiedt meestal per 1000 stenen volgens de C.A.O. De kipkarren worden bij de fabriek afgehaakt en de locomotief gaat met de lege wagens naar de bagger terug.
De kollergang
De volle wagens worden nu één voor één met een lier omhoog getrokken en komen in de “kollergang”. Hier worden ze omgekipt en de klei komt in de beschikker terecht. Dit is een lange transportband die langzaam voortbewogen wordt. De klei valt dan vanaf deze transportband in een ronde ruimte, waarvan de bodem uit roosters bestaat en waarover twee zware ronde walsen rollen.
De rasper
De klei wordt door deze roosters geperst, waardoor de grove stukken wat fijner gemalen worden. Onder deze roosters loopt een draaiende schijf, waarop de pilletjes klei vallen en die door een opening in de opstaande rand rondom deze schijf in de volgende machine vallen. Dit is weer een vermalingmachine, de “rasper”. Het systeem is hier weer hetzelfde als bij de kollergang, alleen met dit verschil, dat in deze machine geen walsen rondlopen, maar een paar zeer stevige armen, die de klei door de roosters rondom de machine persen. Onder deze rasper loopt weer een draaiende schijf die de klei op een transportband werpt. Deze transportband loopt een weinig omhoog en de klei komt van deze transportband af in de steenpers terecht.
De steenpers
Deze machine bestaat uit twee gedeelten. Aan de ene kant een vertragingsbak en aan de andere kant een trechtervormige ronde koker. In deze koker loopt een wormwiel dat de klei in één bepaalde richting voortstuwt. Aan het eind van de pers zit de “steenmond” bevestigd. Dit is een blok ijzer dat taps toeloopt en waardoor de klei geperst wordt.
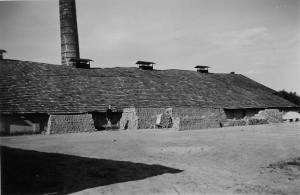
De grootte van het gat in deze mond bepaalt de grootte der stenen. Deze mond zit er los voor, zodat men deze kan vervangen door grotere of kleinere soorten naar gelang de grootte der steen die men wil maken. Ook kunnen in deze mond nopjes worden bevestigd, zodat er ruimten in de klei overblijven. Dit worden dan de “gaatjes stenen”. Deze gaatjes maakt men er in om
twee redenen en wel om het droogproces te bevorderen, de wind kan er dan beter doorheen blazen, en om betere isolatie te verkrijgen. De stenen worden n.l. bij het metselen plat op elkaar gelegd, zodat dus in de muur die men bouwt kolommen stilstaande lucht worden gemetseld en dit is een zeer goede isolatie. De klei is dus nu op de gewenste grootte en de koek, die uit de mond tevoorschijn komt, behoeft alleen nog maar afgesneden te worden. Ze loopt eerst nog een eindje over een transportband, waarop zich een zandmachine bevindt, die zand rondom de koek verspreidt om het aaneen kleven van de stenen in de droogschuren te voorkomen. Dan wordt de koek afgesneden door de knipautomaat, die de stenen op gelijke maat afsnijdt en ze drie aan drie op een klein transportbandje verschuift.
Het drogen van de stenen
Voor deze automaat staat een arbeider, die de stenen aanpakt en ze op een wagentje plaatst, waarop planken liggen. Deze planken zijn opklapbaar, zodat de stenen er gemakkelijk op geplaatst kunnen worden. Deze wagentjes lopen op luchtbanden en worden door een kleine tractor getrokken. Dan komen de stenen in de droogschuren op rekken te staan. De stenen hierop worden los van elkaar geplaatst, zodat de wind er beter doorheen kan waaien wat snel drogen bevordert. Bij harde schrale wind of zeer sterke zonneschijn hangt men jute doeken voor de nog natte stenen, daar ze anders te snel gaan drogen en daardoor gaan scheuren. In deze droogschuren blijven ze ongeveer 14 dagen staan. Dan zit er nog ongeveer een percentage van 10% water in, maar dat is geen bezwaar meer voor het stoken. De stenen worden hierna op wagentjes geladen, die door een paard naar de oven getrokken worden. Dan worden ze in de oven geplaatst. De oven van de fabriek die beschreven wordt is een “ringoven”.
De ringoven
De schoorsteen staat midden op de oven. De ruimte waarin gestookt wordt ligt als een ovale ring om deze oven heen. Hij staat in verbinding met de stookruimte door rookkanalen. Hierop zijn afsluiters geplaatst, zodat men veel of weinig “trek” in de oven kan verkrijgen. Hiermede regelt men ook de voortgang van het vuur.
De oven staat vol stenen, behalve één kamer, dat is de ruimte tussen twee deuren, die voor het in- en uitkruien benut wordt. Door nu bij het achtervuur een rookkanaal af te sluiten en bij het voorvuur er een te ontsluiten zuigt men als het ware het vuur vooruit, zodat dit rond door de oven gaat. De ruimte tussen het vuur en de lege kamer blijft constant, zodat altijd door gestookt kan worden. De kolen worden door de stookgaten van boven naar beneden gegooid. De temperatuur voor deze oven is ±900 °C. Maakt men de temperatuur hoger, dan smelten de stenen en vormen één grote klomp, die er bijna niet uit te halen is. De ruimte tussen gebakken en ongebakken stenen wordt ook zoveel mogelijk constant gehouden. Wat er aan gebakken stenen uitgaat komt er aan ongebakken stenen weer in. De productie van deze beschreven fabriek bedraagt ca. 5.000.000 stenen per jaar.
Gebakken wordt er gedurende het hele jaar, maar geproduceerd alleen tijdens de zomermaanden, daar ’s winters de stenen in de droogschuren zouden bevriezen.
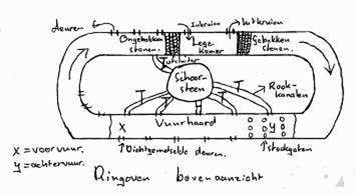
Noten
1 Gegevens ontleend aan de N.V. Bornsche Steenfabriek: v/h H. Morselt
(–> naar PDF-versie van deze publicatie)
(–> naar Inhoudsopgave 2010-01)
(–> naar Boorn & Boerschop pagina)